Кракен продажа
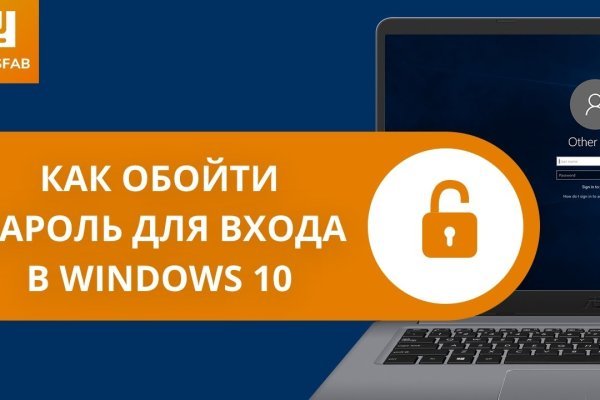
Onion - CryptoParty еще один безопасный jabber сервер в торчике Борды/Чаны актуальная Борды/Чаны nullchan7msxi257.onion - Нульчан Это блять Нульчан! Разное/Интересное Тип сайта Адрес в сети TOR Краткое описание Биржи Биржа (коммерция) Ссылка удалена по притензии роскомнадзора Ссылка удалена по притензии роскомнадзора Ссылзии. Underdj5ziov3ic7.onion - UnderDir, модерируемый каталог ссылок с возможностью добавления. Внутри ничего нет. ( зеркала и аналоги The Hidden Wiki) Сайты со списками ссылок Tor ( зеркала и аналоги The Hidden Wiki) torlinkbgs6aabns. Onion - SwimPool форум и торговая площадка, активное общение, обсуждение как, бизнеса, так и других андеграундных тем. Сайты со списками ссылок Tor. Onion - Daniel Winzen хороший e-mail сервис в зоне.onion, плюс xmpp-сервер, плюс каталог онион-сайтиков. Кардинг / Хаккинг. Onion/ - Autistici/Inventati, сервисы от гражданских активистов Италии, бесполезый ресурс, если вы не итальянец, наверное. Английский язык. Qubesos4rrrrz6n4.onion - QubesOS,.onion-зеркало проекта QubesOS. Onion - the Darkest Reaches of the Internet Ээээ. Legal обзор судебной практики, решения судов, в том числе по России, Украине, США. Поисковики Tor. Onion - Бразильчан Зеркало сайта brchan. Onion - Verified,.onion зеркало кардинг форума, стоимость регистрации. Onion - BitMixer биткоин-миксер. Onion - Checker простенький сервис проверки доступности.onion URLов, проект от админчика Годнотабы. Мы выступаем за свободу слова. Хостинг изображений, сайтов и прочего Tor. Комиссия от 1. Независимый архив magnet-ссылок casesvrcgem4gnb5.onion - Cases. Onion - torlinks, модерируемый каталог.onion-ссылок. Onion - XmppSpam автоматизированная система по спаму в jabber. Onion - Stepla бесплатная помощь психолога онлайн. Литература. Onion - SleepWalker, автоматическая продажа различных виртуальных товаров, обменник (сомнительный ресурс, хотя кто знает). Безопасность Tor.
Кракен продажа - 2krn c
С другой стороны, у него есть версии для iOS, Android, PC и Mac: последние две очень простые в использовании. Вся ответственность за сохранность ваших денег лежит только на вас. Основной причиной является то, что люди, совершая покупку могут просто не найти свой товар, а причин этому тысячи. Гарантия возврата! Заведи себе нормальный антивирус и фаервол, правильно настрой их и научись пользоваться - и спи себе спокойно. Просмотр. Как зарегистрироваться на Mega? Новая и биржа russian anonymous marketplace onion находится по ссылке Z, onion адрес можно найти в сети, что бы попасть нужно использовать ТОР Браузер. Постараюсь объяснить более обширно. Хотя слова «скорость» и «бросается» здесь явно неуместны. Также у каждого продавца на площадке выставлены отзывы от предыдущих сделок. Onion заходить через тор. Сам же сайт включает в себя множество функций которые помогают купить или продать вес буквально автоматизированно, и без лишних третьих лиц. Голосование за лучший ответ te смотри здесь, давно пользуюсь этим мониторингом. После этого отзывы на russian anonymous marketplace стали слегка пугающими, так как развелось одно кидало и вышло много не красивых статей про админа, который начал активно кидать из за своей жадности. Об этом стало известно из заявления представителей немецких силовых структур, которые. Мега Даркнет не работает что делать? Всяческие политико-революционно-партизанские ресурсы здесь не привожу намеренно. Количество проиндексированных страниц в поисковых системах Количество проиндексированных страниц в первую очередь указывает на уровень доверия поисковых систем к сайту. Html верстка и анализ содержания сайта. Onion - Продажа сайтов и обменников в TOR Изготовление и продажа сайтов и обменников в сети TOR. Onion - Freedom Chan Свободный чан с возможностью создания своих досок rekt5jo5nuuadbie. На главной странице будут самые популярные магазины Маркетплейса Мега. Qubesos4rrrrz6n4.onion - QubesOS,.onion-зеркало проекта QubesOS. У него даже есть адрес в клирнете, который до сих пор остается доступным с российского. Kp6yw42wb5wpsd6n.onion - Minerva зарубежная торговая площадка, обещают некое двойное шифрование ваших данных, присутствует multisig wallets, саппорт для разрешения ситуаций. Onion - TorSearch, поиск внутри.onion. Наберитесь терпения и разработайте 100-150 идей для своего проекта. Комплексный маркетинг. Хочу узнать чисто так из за интереса. Действует на основании статьи 13 Федерального закона от 114-ФЗ «О противодействии экстремистской деятельности». Форумы. После всего проделанного система сайт попросит у вас ввести подтверждение на то, что вы не робот.
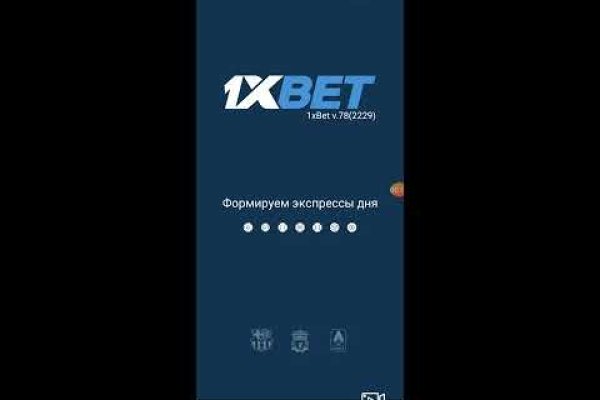
В итоге купил что хотел, я доволен. Ну а, как правило, вслед за новыми зеркалами появляются всё новые мошенники. Уже! RAM 1500 - Автосалон Ramtruck. Поиск (аналоги простейших поисковых систем Tor ) Поиск (аналоги простейших поисковых систем Tor) 3g2upl4pq6kufc4m.onion - DuckDuckGo, поиск в Интернете. Оставляет за собой право блокировать учетные записи, которые. Храм культовое сооружение, предназначенное для совершения богослужений и религиозных обрядов. Омг Вход через Ссылка на Омг - все ссылки. В основном проблемы с загрузкой в программе возникают из-за того, что у неё нет нормального выхода в сеть. Спасибо администрации Омг Onion и удачи в продвижении! Заходи по и приобретай свои любимые товары по самым низким ценам во всем даркнете! В этом видео мы рассмотрим основной на сегодняшний день маркетплейс- Mega Darknet Market (megadmeov(точка)com который встал на место легендарной "трехголовой". Какие бывают виды, что такое психотропные и как они воздействуют. Гобой София Гришина. Список сайтов. Покупки с использованием биткоина без задержки транзакций, блокировки кошельков и других проблем Опция двухфакторной аутентификации PGP Ключи Купоны и система скидок Наличие зеркал Добавление любимых товаров в Избранное Поиск с использованием фильтров. 103 335 подписчиков. Форум Форумы lwplxqzvmgu43uff. Площадь торгового центра. Здесь представлены ссылки и зеркала, после блокировки оригинального. Осенью в мега Белая Дача состоялось открытие пешеходного моста связывающего первое здание со вторым, а также мега была построена в Самаре, но из-за кризиса открытие отложили до 2011 года. Комментарии Boor123 Сегодня Птичка в клетке! Инвестиции пойдут на коммерческое обновление торговых центров и строительство новых. Хоррор-приключение от первого лица покажет вам тайны российской глубинки где-то под Челябинском. Импортеры комплектующих для ноутбуков (матрицы, батареи, клавиатуры, HDD). Дайвинговое снаряжение. Это сделано для того, чтобы покупателю было максимально удобно искать и приобретать нужные товары. Вместе с процесс покупки станет простым, быстрым и приятным! 2006 открытие первой очереди торгового центра «мега Белая Дача» в Котельниках (Московская область). Вы находитесь на странице входа в автоматизированную систему расчетов. Даркмаркет направлен на работу в Российском рынке и рынках стран СНГ. Новый даркнет, mega Darknet. это программа для доступа к облачному хранилищу с автоматической. Книжная лавка, район Советский, улица Калинина: фотографии, адрес. Телефон Горячей линии по Всей России: Звонок Платный. Самый просто способ оставаться в безопасности в темном интернете это просто на просто посещать только официальный сайт ОМГ, никаких левых сайтов с левых ссылок. Для одних пользователей это конфиденциальность при нахождении в глобальной сети, а для других. Самая крупная торговая онлайн-площадка в сети. Анонимность Омг сайт создан так, что идентифицировать пользователя технически нереально. Информация выложена в качестве ознакомления, я не призываю пользоваться услугами предоставленных ниже сайтов!