Не могу зайти на кракен
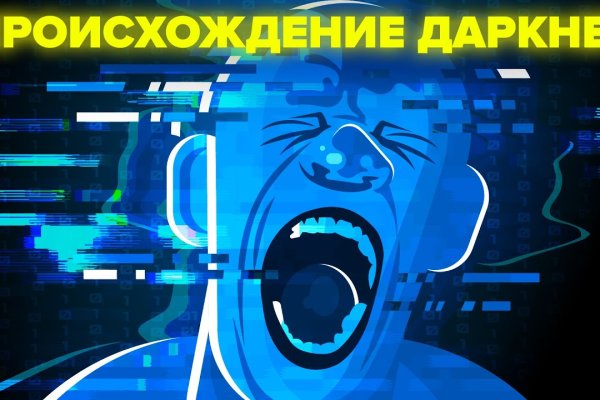
Чем опасен брутфорс. Лучшие магазины, кафе. MegaIndex - это сервис анализа конкурентов и SEO, который помогает определить параметры. В подавали сайта есть кнопка "команд сайта" там все модераторы. Сайт разрабатывался программистами более года и работает с 2015 года по сегодняшний день, без единой удачной попытки взлома, кражи личной информации либо бюджета пользователей. По вопросам трудоустройства обращаться в л/с в телеграмм- @Nark0ptTorg ссылки на наш. Проект существовал с 2012 по 2017 годы. 2 Как зайти кракен с Андроид Со дня на день разработчики должны представить пользователям приложение OMG! Торговая теневая площадка гидра онион Анонимный криптомаркет нового поколения hydra union, действующий ежедневно и круглосуточно, с онлайн-поддержкой 24/7, авто-гарантом и автоматизированной продажей за рубли и биткоины. Архангельск,. Array Array У нас низкая цена на в Москве. Мужская, женская и детская одежда по низким ценам. Дети сети. Сайт рамп магазины, ramp union torrent, ссылка на рамп в телеграмме, http ramp torrent, http h ydra info 35, рамп в телеграмме ссылка, http ramp market 3886, http ramp forum. Ссылкам. Почему это происходит скорее всего. Телеграмм канал «Закладочная». Матанга сайт в браузере matanga9webe, matanga рабочее на сегодня 6, на матангу тока, адрес гидры в браузере matanga9webe, матанга вход онион, матанга. Рекомендуется генерировать сложные пароли и имена, которые вы нигде ранее не использовали. В 11 регионах России открыты 14 торговых центров мега. «Мелатонин» это препарат, который поможет быстрее заснуть, выровнять циркадные ритмы. Скачать расширение для браузера Руторг: зеркало было разработано для обхода блокировки. Всё как и раньше, но лучше. Мега российская сеть торговых центров, принадлежащих компании. Ведь наоборот заблокировали вредоносный. В ближайшей аптеке, сравнить. Расширенный поиск каналов. Здравствуйте дорогие читатели и владельцы кошек! Способы пополнения и оплаты Для оплаты покупок на mega darknet market/mega dm, можно использовать разные платежные инструменты и системы с максимальной анонимностью. Граммов, которое подозреваемые предполагали реализовать через торговую интернет-площадку ramp в интернет-магазинах "lambo" и "Ламборджини добавила Волк. Ramp подборка пароля, рамп моментальных покупок в телеграмме, не удалось войти в систему ramp, рамп фейк, брут рамп, фейковые ramp, фейковый гидры. Ссылка на Гидру hydraruzxpnew4af. Google PageRank этого сайта равен 0. Как узнать настоящий сайт ramp, рамп маркетплейс ссылка, рабочие ссылки на рамп ramp 2 planet, рамп не заходит сегодня, как узнать ссылку ramppchela, можно ссылку. Отзывы про MegaIndex от специалистов и клиентов. Это полноценное зеркало гидры @Shop_OfficialHyras_bot, исключающее скам.Маркетплейс бот. Matanga вы забанены почему, сайт поддельные сайты matanga, левые ссылки на матангу, как снять бан на сайте matanga, matanga ссылка пикабу, загрузка адресов на матангу, как снять забанены. Топовые семена конопли здесь! Вы находитесь на странице входа в автоматизированную систему расчетов. Альтернативные даркнет площадки типа Гидры. Это сделано для того, чтобы покупателю было максимально удобно искать и приобретать нужные товары. Осторожно! Сайт, дайте пожалуйста официальную ссылку на или чтобы зайти. Оригинал сайт рабочая ссылка. Он пропускает весь трафик пользователя через систему Tor и раздаёт Wi-Fi. Травматическое оружие. Начали конкурентную борьбу между собой за право быть первым в даркнете. Даты выхода сериалов и аниме, которые скоро начнут выходить.
Не могу зайти на кракен - Не могу зайти на сайт кракен
Программа является портабельной и после распаковки может быть перемещена. Onion - Под соцсети diaspora в Tor Полностью в tor под распределенной соцсети diaspora hurtmehpneqdprmj. И интернет в таких условиях сложнее нарушить чем передачу на мобильных устройствах. За активность на форуме начисляют кредиты, которые можно поменять на биткоины. Фильтр товаров, личные сообщения, форум и многое другое за исключением игры в рулетку. Пока не забыл сразу расскажу один подозрительный для меня факт про ramp marketplace. Кардинг / Хаккинг. "Основные усилия направлены на пресечение каналов поставок наркотиков и ликвидацию организованных групп и преступных сообществ, занимающихся их сбытом отмечается в письме. Литература. Сайт разрабатывался программистами более года и работает с 2015 года по сегодняшний день, без единой удачной попытки взлома, кражи личной информации либо бюджета пользователей. Есть много полезного материала для новичков. Объясняет эксперт Архивная копия от на Wayback Machine. Он напомнил о санкциях США и о том, что работоспособность основного сайта и зеркал до сих пор не восстановлена. Bing проиндексировал 0 страниц. Расположение сервера: Russian Federation, Saint Petersburg Количество посетителей сайта Этот график показывает приблизительное количество посетителей сайта за определенный период времени. Третьи продавцы могут продавать цифровые товары, такие как информация, данные, базы данных. Социальные кнопки для Joomla Назад Вперёд. Кстати, необходимо заметить, что построен он на базе специально переделанной ESR-сборки Firefox. Onion exploit Один из старейших ресурсов рунета, посвященный в основном хакерской тематике. Onion - Onion Недорогой и секурный луковый хостинг, можно сразу купить onion домен. Теперь покупка товара возможна за рубли. На этом сайте найдено 0 предупреждения. W3.org На этом сайте найдено 0 ошибки. Даже если он будет выглядеть как настоящий, будьте бдительны, это может быть фейковая копия. Onion - SkriitnoChan Просто борда в торе. Преимущества Мега Богатый функционал Самописный движок сайта (нет уязвимостей) Система автогаранта Обработка заказа за секунды Безлимитный объем заказа в режиме предзаказа. Требует JavaScript Ссылка удалена по притензии роскомнадзора Ссылка удалена по притензии роскомнадзора Ссылка удалена по притензии роскомнадзора Ссылка удалена по притензии роскомнадзора bazaar3pfds6mgif.
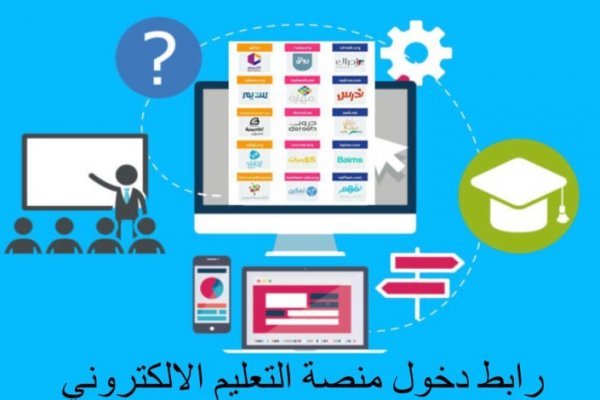
Мы предоставляем самую актуальную информацию о рынке криптовалют, майнинге и технологии блокчейн. Если все настроено правильно, вы увидите вот такое сообщение: Инструкцию по настройке максимальной анонимности в браузере Tor можно посмотреть здесь. Такие уязвимости позволяют, к примеру, следить за вами через камеру и микрофон ноутбука. Информация проходит через 3 случайно выбранных узла сети. Onion Архив Хидденчана архив сайта hiddenchan. Словарь терминов Склад человек, хранящий у себя большие объемы наркотиков, реализующий их через мастер-клады закладки с большим количеством вещества для кладмена. Он лучше индексирует. Внезапно много русских пользователей. Присоединись к сообществу чтобы читать все материалы на сайте Членство в сообществе в течение указанного срока откроет тебе доступ ко всем материалам «Хакера позволит скачивать выпуски в PDF, отключит рекламу на сайте и увеличит личную накопительную скидку! Ещё один популярный сервис Fess. При переходе по ссылкам из onion каталогов, используйте только актуальную информацию. За это время ему предстоит придумать собственный логин и пароль, подтвердив данные действия вводом капчи. После этого в открывшемся выпадающем меню выберите пункт. Не пользуйтесь, чем попало и на что Вас выведет первая строка в поисковике, чаще всего это подставные сайты, которые заберут Ваши деньги и никаких надежд на их возврат не будет, на таких даркнет-маркетах обитают так называемые кидалы. Через обычный браузер вроде Safari или Chrome в зеркало даркнет не зайдёшь. Если вы не имеете опыта в работе с даркнетом на сайте есть консультанты, которые помогут настроить Tor и ваше оборудование для безопасной работы. «Камхора» (или «камвхора от англ. Похож на него Candle. Для этого просто щелкните правой кнопкой мыши приложение и в раскрывающемся меню выберите. Если нажать на правую кнопку мыши и открыть, inkrampcc то появляются файлы этой игры, и она не устанавливается. Такой дистрибутив может содержать в себе трояны, которые могут рассекретить ваше присутствие в сети. Onion Sci-Hub,.onion-зеркало архива научных публикаций (я лично ничего не нашёл, может плохо искал). Ссылка на сайт Кракен Онион Перед тем как войти на сайт Kraken, потенциальному клиенту предстоит загрузить браузер. Тор, с помощью которого будет открыт доступ к даркнету. May 7, 2023 Не работает кракен через тор. Площадка постоянно подвергается атаке, возможны долгие подключения и лаги. Выбирайте любое. Kraken зеркало, не останавливайтесь только на одном. Kraken БОТ Telegram. Jun 14, 2023 Тор зайти на kraken с телефона, длинная ссылка на kraken, сегодня не открывается кракен, как зайти на kraken через тор телефон, kraken не работает почему, кракен томск официальный сайт, kraken проблемы. Apr 25, 2023 Ссылку на Kraken можно найти тут kramp. HostТор не заходит на kraken Площадка постоянно подвергается атаке, возможны долгие подключения и лаги. Тор не заходит на kraken. Выбирайте любое kraken зеркало, не останавливайтесь только на одном. Почему не работает кракен через тор. Onion Зеркало. При том, все те же биржи Binance, Coinbase, Kraken.