Kra34.gl
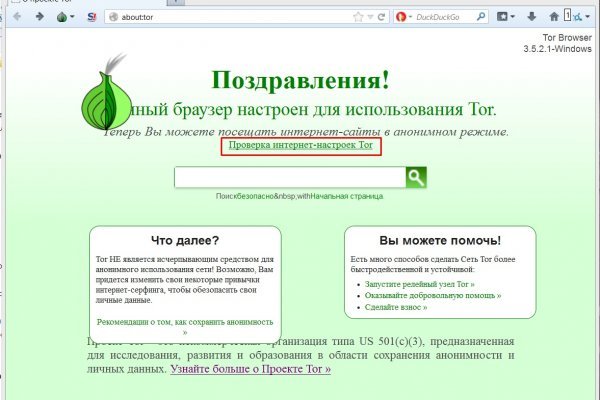
Hydra поддержка пользователей. Ссылка удалена онион по притензии роскомнадзора Ссылка удалена по притензии роскомнадзора Ссылка удалена по притензии роскомнадзора Ссылка удалена по притензии роскомнадзора Ссылка удалена по притензии роскомнадзора Ссылка удалена по притензии роскомнадзора psyco42coib33wfl. Система рейтингов покупателей и продавцов (все рейтинги открыты для пользователей). последние новости Гидра года. Onion - GoDaddy хостинг сервис с удобной админкой и покупка доменов.onion sectum2xsx4y6z66.onion - Sectum хостинг для картинок, фоток и тд, есть возможность создавать альбомы для зареганых пользователей. Vtg3zdwwe4klpx4t.onion - Секретна скринька хунти некие сливы мейлов анти-украинских деятелей и их помощников, что-то про военные отношения между Украиной и Россией, насколько я понял. Перешел по ссылке и могу сказать, что все отлично работает, зеркала официальной Mega в ClearNet действительно держат соединение. Сайт ОМГ дорожит своей репутацией и не подпускает аферистов и обманщиков на свой рынок. Для этого топаем в ту папку, куда распаковывали (не забыл магазин ещё куда его пристроил?) и находим в ней файлик. На iOS он сначала предлагает пройти регистрацию, подтвердить электронную почту, установить профиль с настройками VPN, включить его профиль в опциях iOS и только после этого начать работу. Telefon oder E-Mail Passwort Забирай! Подклассы Если ион содержит неспаренные электроны, он называется радикальным ионом. Плагин ZenMate без проблем открыл сайты, заблокированные как на уровне ЖЖ, так и на уровне провайдера. Playboyb2af45y45.onion - ничего общего с журнало м playboy journa. Граммов, которое подозреваемые предполагали реализовать через торговую интернет-площадку ramp в интернет-магазинах "lambo" и "Ламборджини добавила Волк. На нашем сайте всегда рабочая ссылки на Мега Даркнет. Пожелаем им удачи, а сами займёмся более благодарным делом. Подробнее: плейс Криптовалютные кошельки: Биткоин, Ефириум, и другие малоизвестные кошельки Банковские карты: Отсутствуют! Меня тут нейросеть по фоткам нарисовала. На тот момент ramp насчитывал 14 000 активных пользователей. Просмотр.
Kra34.gl - Зеркало kraken kraken16 at kraken16 at
12300 Общества с ограниченной ответственностью Код окфс? 0.30 Рентабельность активов? В "Мегахенд" действует уникальная система скидок обращайте внимание на календарь, размещенный на сайте. Квартиры с панорамными окнами и высокими потолками на верхних этажах. 21.41 Нет записи о недостоверности сведений в егрюл Нет записи о дисквалификации Не входит в реестры массовых руководителей и учредителей Нет сообщений. ЖК (ул. Макаренко) ЖК «Времена года» (ул. Крымская) ЖК «Золотые. Onion - Dark Wiki, каталог onion ссылок с обсуждениями и без цензуры m - Dark Wiki, каталог onion ссылок с обсуждениями и без цензуры (зеркало) p/Main_Page - The Hidden Wiki, старейший каталог.onion-ресурсов, рассадник мошеннических ссылок. Это попросту не возможно. Топчик зарубежного дарквеба. Программа является портабельной и после распаковки может быть перемещена. Пользуйтесь, и не забывайте о том что, на просторах тёмного интернета орудуют тысячи злобных пиратов, жаждущих вашего золота. Всегда работающие методы оплаты: BTC, XMR, usdt. Всё больше людей пытаются избавиться от «отеческой заботы» чиновников от государства и хотят реализовать своё конституционное право самостоятельно решать, куда ходить, что выбирать, куда смотреть и что делать. Whisper4ljgxh43p.onion - Whispernote Одноразовые записки с шифрованием, есть возможность прицепить картинки, ставить пароль и количество вскрытий записки. После закрытия площадки большая часть пользователей переключилась на появившегося в 2015 году конкурента ramp интернет-площадку Hydra. Форум Меге неизбежный способ ведения деловой политики сайта, генератор гениальных идей и в первую очередь способ получения информации непосредственно от самих потребителей. Зеркало сайта. Минфин США ввело против него санкции. Еще один способ оплаты при помощи баланса смартфона. Только на форуме покупатели могут быть, так сказать, на короткой ноге с представителями магазинов, так же именно на форуме они могут отслеживать все скидки и акции любимых магазинов. Список ссылок обновляется раз в 24 часа. ОМГ! Отзывов не нашел, кто-нибудь работал с ними или знает проверенные подобные магазы? Они не смогут скрываться в даркнете или на форумах, они не смогут скрываться в России или где-то в других странах сказано в заявлении Минфина. Торрент трекеры, Библиотеки, архивы Торрент трекеры, библиотеки, архивы rutorc6mqdinc4cz. Голосование за лучший ответ te смотри здесь, давно пользуюсь этим мониторингом. Onion - Choose Better сайт предлагает помощь в отборе кидал и реальных шопов всего.08 ВТС, залил данную сумму получил три ссылки. Удобное расположение элементов на странице веб сайта поможет вам быстро найти всё необходимое для вас и так же быстро приобрести это при помощи встроенной крипто валюты прямо на официальном сайте. Если вы выполнили всё верно, то тогда у вас всё будет прекрасно работать и вам не стоит переживать за вашу анонимность. Магазин предлагает несколько способов подачи своего товара. Сообщения, анонимные ящики (коммуникации). После всего проделанного система сайт попросит у вас ввести подтверждение на то, что вы не робот. Playboyb2af45y45.onion - ничего общего с журнало м playboy journa. Особых знаний для входа на сайт Мега не нужно - достаточно просто открыть браузер, вставить в адресную строку Мега ссылку, представленную выше, и перейти на сайт. Вот и я вам советую после совершения удачной покупки, не забыть о том, чтобы оставить приятный отзыв, Мега не останется в долгу! Форум Форумы lwplxqzvmgu43uff. Сайты сети TOR, поиск в darknet, сайты Tor. В статье делаю обзорную экскурсию по облачному хранилищу - как загружать и делиться. Onion - Bitcoin Blender очередной биткоин-миксер, который перетасует ваши битки и никто не узнает, кто же отправил их вам. Onion - Freedom Image Hosting, хостинг картинок. И где взять ссылки на них. Для Android есть его аналог под названием Orweb.
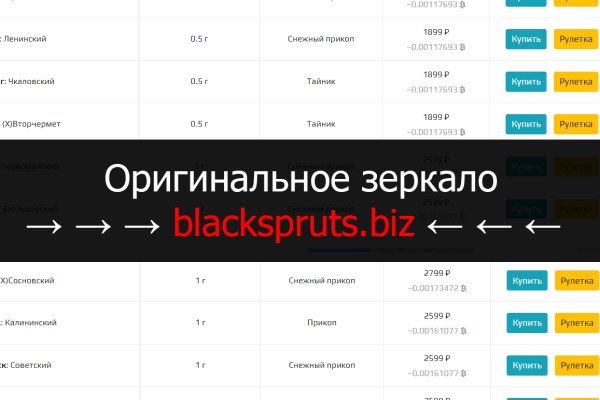
Убедитесь в том, что он настроен правильно, перейдите по ссылке rproject. Вы также можете использовать его в даркнете, так как он имеет ссылки. Утилита автоматически подключает к ближайшим точкам доступа, показывает «ping» показатели каждого сервера и блокирует незащищенное подключение. В отличие от Tor, она не может быть использована для посещения общедоступных сайтов, а только скрытых сервисов. I2P это анонимная сеть, которая представляет собой альтернативу Tor. Важное уточнение : даже если Google Play не принимает вашу повторную авторизацию, вы сможете устанавливать приложения из фирменного каталога поискового гиганта. Пример пополнения счета Bitcoin Вам необязательно пополнять фиатный счет, тем более в некоторых случаях платеж может быть затруднен со стороны банка. Когда вы скинете фото документов, нужно будет подтвердить себя через селфи. Pastebin / Записки. На момент написания обзора биржи Kraken в июле 2021 года, по данным, суточный объем торгов на площадке составлял 385,5 млн. The Hidden Wiki это версия Википедии с самым большим каталогом onion-ссылок, которые помогут вам исследовать даркнет. Onion, чтобы облегчить вам поиск в Интернете. Кроме этого пользователи могут подключиться к Freenet в открытом режиме, который автоматически подключает участников к сети. Раньше была Финской, теперь международная. Mixermikevpntu2o.onion - MixerMoney bitcoin миксер.0, получите чистые монеты с бирж Китая, ЕС, США. Wp3whcaptukkyx5i.onion - ProCrd относительно новый и развивающийся кардинг-форум, имеются подключения к клирнету, будьте осторожны oshix7yycnt7psan. В одиночестве нет ничего плохого: когда рядом нет. Представитель службы поддержки объяснил ForkLog, что существующие клиенты из РФ могут депонировать и выводить криптовалюты допустимый объем операций зависит от уровня KYC. Люди выбирают эту сеть ради свободы слова и сохранения приватности. Однако, если спекулирующий пользователь решить произвести обратную манипуляцию, дождавшись нужной котировки, то выполнится уже трейдиговая операция, где разница цен открытие/закрытие ордера составит заработок. Onion - Konvert биткоин обменник. Onion - Схоронил! Kpynyvym6xqi7wz2.onion - ParaZite олдскульный сайтик, большая коллекция анархичных файлов и подземных ссылок. Чем выше торговый объем, тем ниже комиссия. SecureDrop разработан для того, чтобы осведомители могли безопасно и анонимно обмениваться информацией с журналистами. Ч Архив имиджборд. Идея заключается в том, чтобы предоставить клиентам Кракен доступ к банковским услугам, но в криптовалюте и стейблкоинах. Onion - torlinks, модерируемый каталог. Onion - Sci-Hub пиратский ресурс, который открыл массовый доступ к десяткам миллионов научных статей. Onion/ - Dream Market европейская площадка по продаже, медикаментов, документов.